Amine gas treating, also known as Ammonia treatment, is a patented chemical process for extracting active amines from natural gas. Ammonia is generated by alkaline hydrolysis of paraffinic waxes (paraffin waxes) and fatty acids. The ammonia removes the amines using an amine-reactive extraction solvent. And then, the extracted amines help manufacture pharmaceuticals, dyes, and pigments.
The most common amines used in the amine scrubbing system process are Monoethanolamine (MEA), Diethanolamine (DEA), and Methyldiethanolamine (MDEA). According to Carver Pump, these three chemicals effectively remove hydrogen sulfide from the treated stream. That said, here are the basic steps of amine gas treatment.
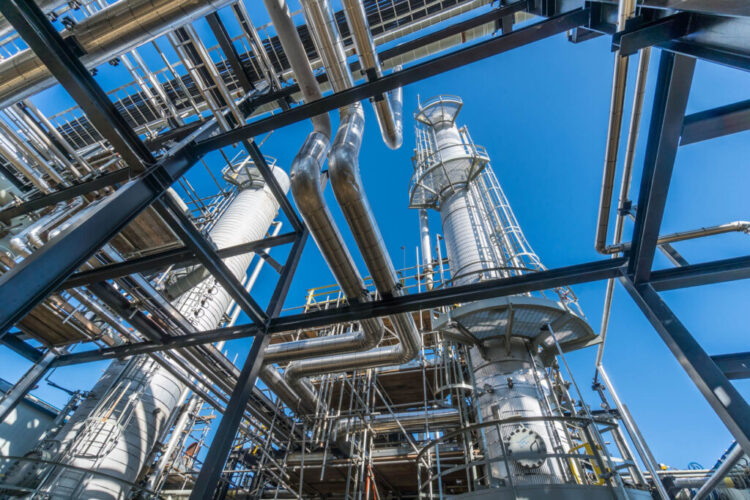
1. Chemical Reaction
The first step of amine gas treatment is the chemical reaction. This reaction occurs between the amine and the acid gas. In this process, the amine reacts with the hydrogen sulfide to form a sulfonate salt. And then, the carbon dioxide reacts with the amine to form a carbamate. These reactions are exothermic, meaning they release heat.
The heat helps to drive the reactions and remove the impurities from the natural gas. Amine gas treating is an essential process for the oil and gas industry. It removes hydrogen sulfide and carbon dioxide from natural gas. This process is necessary for the safety of workers and the environment.
2. Absorption
Absorption is the second step of amine gas treatment, and it is where the majority of the gas removal takes place. In this step, the amine solution contacts the natural gas stream, and the amine molecules bind to the acidic gases in the stream. As the amine-rich solution flows through the absorption tower, it removes more acid gas from the natural gas stream.
The final product is a clean natural gas stream that meets pipeline specifications. The acid-laden amine solution is then sent to a stripper, where the acid gases are removed from the solution so people can reuse them. Because absorption is such an important step in gas treatment, it is essential to have a high-quality absorption tower to achieve optimal results.
3. Desorption
Desorption is the third step in amine gas treatment. In this step, the amine is regenerated by stripping it from the sour gas. You can do this using steam, which removes any other contaminants that may have adsorbed onto it. The stripped amine is then cooled and recycled back to the absorption step, where you can use it again.
Desorption is essential in amine gas treatment because it allows the amine to be reused. It helps to improve the efficiency of the process and reduces the overall cost. Additionally, it helps to ensure that the treated gas is free of impurities and safe for release into the atmosphere.
4. Stabilization
After the amine gas treatment has removed the hydrogen sulfide (H2S) and carbon dioxide (CO2) from the natural gas, the next step is stabilization. Stabilization is a process that removes any remaining impurities such as water, hydrocarbons, and solids before the natural gas is sent to storage or pipelines. The first step in stabilization is to remove any free water from the gas. You can do this with a dehydration unit, which uses pressure and heat to remove the water. Next, you must remove any dissolved water.
You can do this with a stripper, which uses a series of trays to remove the dissolved water. After the water has been removed, the next step is to remove any remaining hydrocarbons. You can do this with an absorption unit, which uses a solvent to absorb the hydrocarbons. Finally, you must remove any solids from the gas. You can do this with a filter, which eliminates any solid particles from the gas.
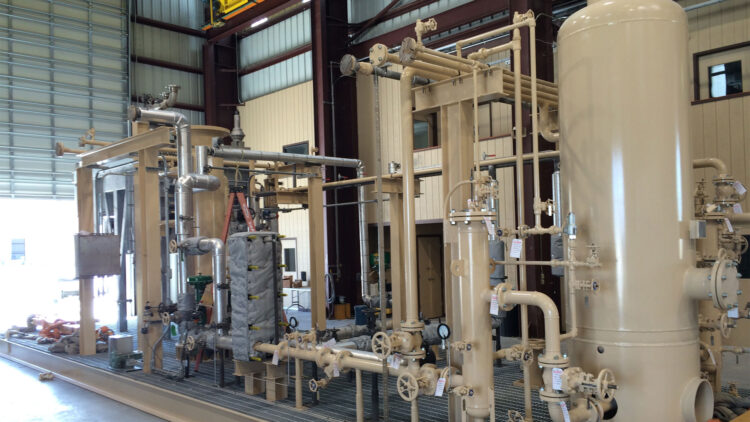
5. Regeneration
Regeneration removes the contaminants from the amine solution so you can reuse them. The most common method of regeneration is stripping. It involves heating the amine solution and using steam to strip the contaminants. The contaminated vapor is then sent to a stripper tower, where it is condensed and removed from the system.
The purified amine solution is then cooled and returned to the absorption tower so people can use it again. Although it takes energy to strip the contaminants out of the amine solution, this method is still more cost-effective than disposing of the contaminated solution and starting with a fresh amine. As a result, regeneration is integral to the amine gas treating process.
6. Purification
Now that the rich amine gas has been stripped of its contaminants, it’s time for purification. This step ensures that the gas is free of residual impurities before it’s used or released into the atmosphere. There are a few different ways to purify amine gas, but ‘scrubbing’ is the most common method. It involves passing the gas through a solution of water and chemicals.
The impurities in the gas will be attracted to the solution, leaving the gas much purer. Once the gas has been purified, you can use it for various purposes, such as fuel for power plants or industrial boilers. It can also be released into the atmosphere, where it will quickly dissipate and pose no threat to human health or the environment.
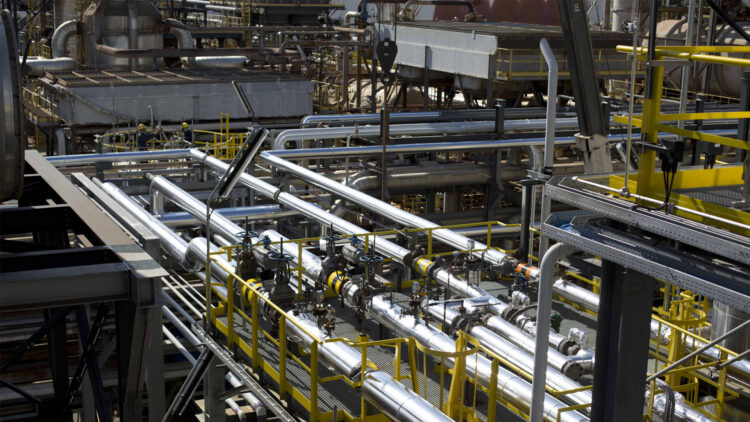
7. Recovery
During this step, the amine solution is separated from the gas stream and recycled back to the contactor. Then, the recovered amine is cooled and reheated to prepare it for the next cycle. Two systems are used for amine recovery: a stripper system and a boiler system. In a stripper system, the amine-rich gas stream passes through a stripping column where the amine is vaporized and separated from the gas.
In a boiler system, the amine-rich gas stream passes through a boiler where the amine is distilled off and condensed. Recovery systems minimize energy consumption and maximize amine reuse. As a result, they play an essential role in ensuring that amine gas treatment is efficient and cost-effective.
8. Reclamation
Reclamation is the process of removing impurities from the amine solution so that you can use it again. It’s typically done by passing the solution through a series of filters and then subjecting it to a process known as regeneration. Regeneration involves heating the solution to remove any remaining impurities. Once the solution has been purified, it can be reused in the amine gas treating process.
Reclamation is an essential step in amine gas treating because it helps improve the overall efficiency of the process. Removing impurities from the amine solution can be reused multiple times, reducing the waste generated by the process. In addition, reclamation helps to reduce the cost of amine gas treatment by eliminating the need for disposable waste solutions.
Takeaway
The amine gas treating process involves eight steps: absorption, stripping, regeneration, purification, recovery, reclamation, and disposal. Each step is vital in ensuring the process is effective and efficient. Amine gas treating is complex, but understanding the basics can help you appreciate its importance in the natural gas industry. By knowing how amine gas treating works, you can be sure that your gas is safe for use and release into the atmosphere.