Laser engraving is the latest technology of engraving materials, that enables the production of even the most demanding products. High precision enables the marking of small parts, as well as the accuracy of cutting various shapes. A feature of laser engraving is that laser radiation either removes surface layers – or contributes to changing their color or structure. However, in this business, you need to be precise, but also have a gift for aesthetics. Therefore, we present 5 tips and tricks for laser engraving and cutting.
What Is Laser Engraving?
Engraving with the help of a laser is a process in which the material exposed to the laser beam and is ignited, melted, and evaporated. This process is clean. There is no contact, it is moisture-free, flexible, and very economical. The laser has been a good ally serving us for many years, especially when it is about engraving work and laser marking of metals – but also other materials such as wood, plastic, etc. In many production branches, products made of these materials are marked with a laser. The application is able to do various things, from marking the industrial serial products – to personalizing promotional products that should contain a logo or names.
How Does It Function?
The laser beam stimulates the evaporation of a thin layer of material from the very surface – which in turn creates special contours
on its surface. As a rule, this type of engraving and cutting have high resolution, quality – and extremely stable images that other printing methods cannot provide. Due to its high precision – quite complex images will be obtained. The benefit of branding products with laser engraving, compared to any other printing – is that it is impossible to remove or damage the engraving. It is because, during the engraving process – the layer of material where the laser passed is removed. Imprint, that is, engraving is very resistant to chemicals, UV radiation, or scratches.
Laser Cutting And Engraving
Laser technology enables printing on various non-metallic materials such as wood, leather, plastic, rubber, glass, marble, etc.
Laser Engraving And Wood Cutting
With laser cutting, you can make and engrave toys, gifts for the New Year and Christmas, works of art and handicrafts, souvenirs, pendants, wooden business cards, and similar things. The thickness of the wood is not crucial for quality engraving because the laser engraves the wood at different depths and so that an extremely clean and clear impression is obtained. Wood suitable for laser printing consists of MDF, plywood, plywood, natural wood, cork, etc.
Laser Plastic Engraving
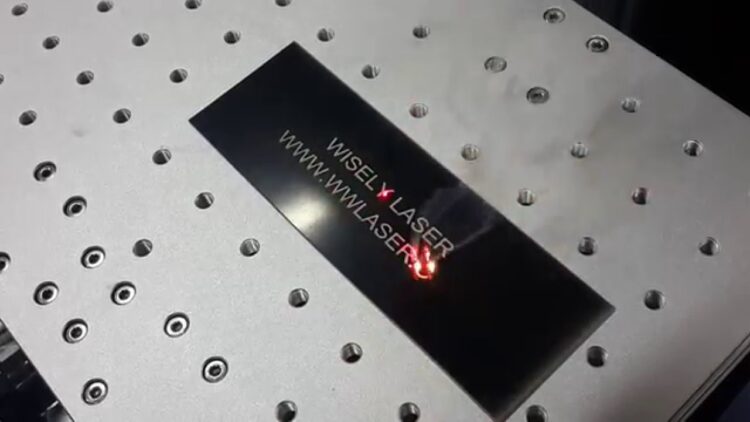
Laser cutting and engraving of plastic are most often done on acrylic materials such as plexiglass. In modern companies such as dxtech.com, you can laser cut plexiglass and plastic – as well as engrave products made of plastic materials. Cutting of these materials is done without touching the laser and the surface of the material, the process itself is clean, and without damaging the cut object. Laser plastic engraving is possible and recommended for making promotional material. You can engrave ballpoint pens, pendants, lighters, and the like.
Practical Tips When Performing Laser Engraving
1. Preparation – The Surface Protection
Whether you wish to cut or maybe to engrave something – you must know that engraving smoke may contaminate the parts of the surface that you’re working on. If you want to avoid that – then you oughta cover such a surface with protective tape. You shouldn’t use the simple adhesive tape because it will not significantly reduce the laser power. Instead of that, use the protective tape which will be very efficient, especially around the engraving area. After you finish performing the engraving process – remove the mask. Professionals use this technique especially when engraving leather.
2. Preset Features
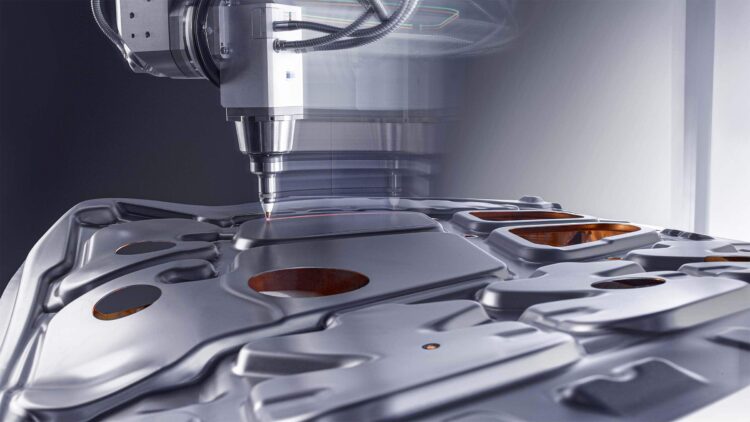
Your laser cutting and engraving machine certainly have some pre-determined settings for working on various materials – but also for different cutting thicknesses and depth of the impression you are making. However, customer requirements are different, so you will probably have a request to enter certain settings yourself according to customer orders and the materials required to make the cut or print. What is important is that you can enter this new data into the machine itself or the computer – and create a separate file. This way you will have saved data that you may need later – and you will be able to easily find it in advance and then use it.
3. Test Cutting
This is a very significant piece of advice because you will definitely not run into the process right away and make a mistake while doing serial production. Even when you have pre-determined parameters for working on a particular material – you should do something we call a test cut. Therefore, it is advisable to make a small sign like a circle or a square – and then try to cut it by using some old material that is a waste residue. Then you will see if there are any problems or shortcomings in the process – or if you need to increase or perhaps decrease the power of the machine before starting it for final work.
4. Layered Work
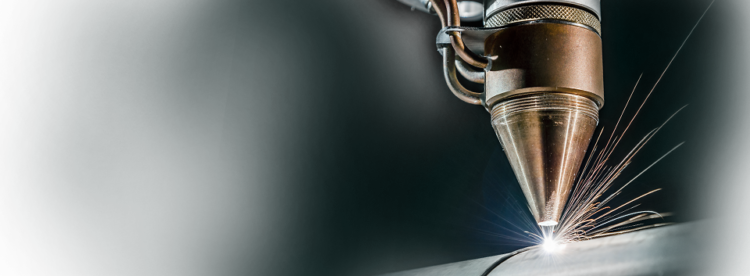
Sometimes, depending on the job itself – the engraving process may be done partially. This means you have the possibility of printing only one part of the complete design or file. How to do that? It’s actually simple. The simplest method is to make, that is, design different parts and then separate them into different layers in your file. The large number of graphics programs used in this process gives you the ability to create different layers that you can then turn on and off as needed. This mode will provide you to manage the cutting order, or to create multiple designs – and you will also be able to create some of your own guides to set up a design.
5. The Distinction Between The Solid And Composite Materials
Take for example that you have a pre-designed logo – so now you wish to make an imprint on a wooden structure. Although wood is an excellent material for things such as engraving – you still must know the distinction when working on a solid piece of wood or using some of the composite materials such as plywood or median. First of all, you must know that natural wood is never uniform. Therefore, you will certainly always get better results if you print on composite materials such as MDF – where the surface is more even.