When a design has been made, a prototype is manufactured to estimate the feasibility of the design. To create the prototype, some amount of manufacturing technology development is necessary. Some people may think that once a design has been proven, the product can be mass-manufactured just like that since the technology for creating the prototype of the established design already exists. If you are interested in this topic, you may click here.
Why And What Kind Of Work Is Required?
The main reason why such a mistake occurs is due to the fact that the amount of product to be manufactured greatly influences the way the product is manufactured. For example, when creating 1-10 plastic parts, it is better to manufacture soft casting tools that are not as durable but quite cheap. They will be enough to create the required volume, but not much more. The time for manufacturing each part will be quite high due to the fact that no automation or process planning is carried out because it would just take too much time to develop them. Some high-level technology development is just not needed because only ten parts are necessary.
However, that is not true when manufacturing volumes reach millions of parts. This is where thorough preparation is necessary. The reason for that is the fact that the number of parts multiplies every manufacturing time unit saved. Let’s say that material loading automation requires 4 hours to be created and decreases the overall process time by 2 seconds. If the product volume is just ten parts, you get to save 20 seconds, which is just not worth it considering the time it takes you to develop the automation system. Things change when we talk about creating 2 million parts, for example. More than a thousand hours is saved when optimizing the process by only 2 seconds! The same can be said about the material required and the waste that is produced. Every gram saves you millions in perspective.
Now, the prototype is manufactured with the idea that only one or two such parts are required. That is why the process is not optimized. It does not use any high-efficiency specialized tooling, automation, and the initial stock manufacturing method may not exist at all. Those are all the potential things that need to be considered when the process of moving to full-scale production is executed.
The Initial Stock Manufacturing Process
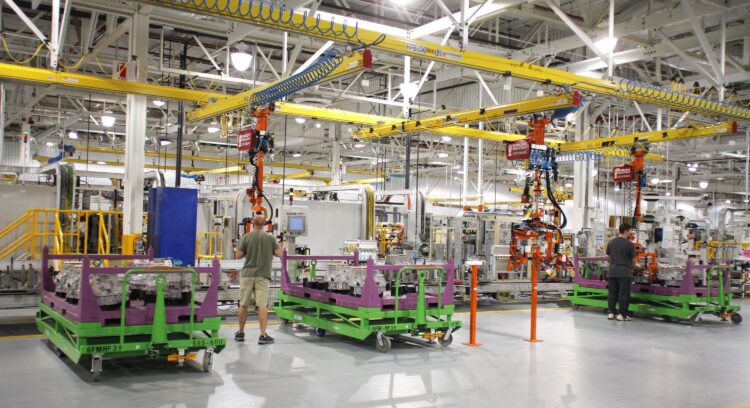
Most prototyping processes use existing standard stocks. Those processes are very useful because you don’t have to create any tooling or any actual blank production yourself. However, when using such stocks, the amount of wasted material is colossal. Up to 60% may go into chips. This makes the actual machining process much longer, and the amount of wasted material will simply make the final part cost too expensive. This is why designing blank production is the first and, most often, the most efficient way to decrease the manufacturing costs of the product. It should be considered that the more money is put into the blank production process, the cheaper each part becomes. Therefore, the more parts you make, the more complex and expensive the blank production must be. For example, when manufacturing turbine blades, the initial stock is so precise and close to the final part that is only finishing processes are required. Injection molds can be created using different materials, and the more durable the mold is, and the more precise, the less additional processing will be required, and if the mold is broken, a lot of money is put into manufacturing a new one. That is why such things are usually calculated beforehand.
Machining And Process Planning
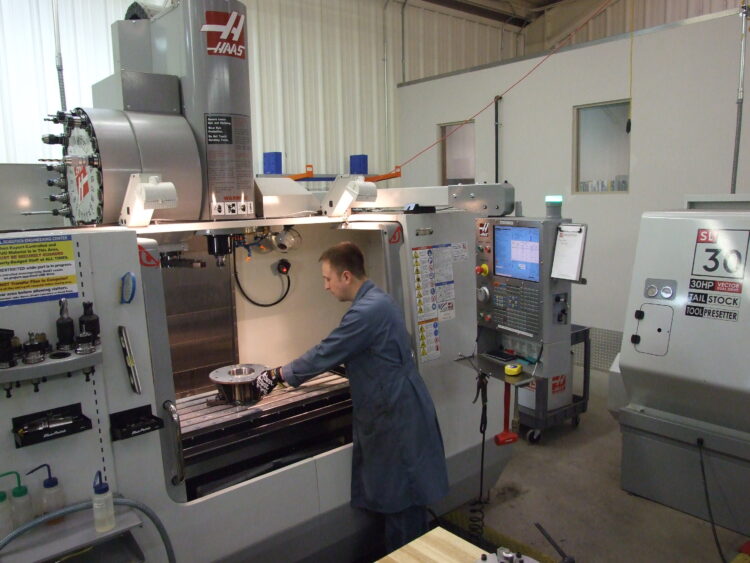
When manufacturing prototypes, the machining process is usually carried out at one or two machine tools. This is due to the fact that it is not viable to have a lot of machine tools when you only make one or two parts at a time. Other tools will just stand without any work. It is better to tune the machine tool a number of times for every machining operation rather than use a lot of tools tuned for every operation. However, this cannot be used in mass production. It is just impossible to create a million parts on one machine tool in a year. That is why a total manufacturing time is calculated for every operation and is multiplied by the number of parts. That way, the total time for every operation is known. Depending on the time required, it may be necessary to buy additional machine tools for the longest operations so that other lathes or CNC centers do not have to wait, so that production does not have bottlenecks. In addition, tuning tools must be brought to a minimum. It is much better to set up every tool for its operation for a year than changing it back and forth and wasting time. After that, it may be important in some cases to move the tools around the factory so that corresponding operations are close together. It will minimize the time required to move the part form operation A to operation B. And finally, every operation is optimized. Specialized automatic fixtures are created in order to minimize clamping time, which may take up to 40% of the total machining time. Tool paths are optimized too so that no useless motions are made and no time is wasted.
Conclusions
Prototyping and mass production technologies are completely different. When prototyping aims at using as many standard elements and fewer tools as possible, mass production aims at creating specialized operations, tools, and technologies in order to minimize each part production time. When prototyping aims at using standard blanks in order to minimize the tools that may be required to produce them, the mass production aims to have its own blank production in order to minimize material waste. To summarize, mass production requires extensive optimization, development, and process planning in order to make it more efficient.