Do you know who works at the Amazon warehouse today? These are mostly robots. With that, don’t forget that Amazon’s warehouse is the same place where workers were afraid of losing their jobs because of mechanical replacements. Today, in this article, we’ll discuss how these robots are impacting human workers and the relationship they share. Read on!
As said earlier, initially, the human workers were afraid of losing their jobs, but now the scenario is different. Today, workers have new fears. Obviously, sharing workspace with a robot is not easy. In fact, these robots are bringing new types of stress and strain in the form of injuries and the malaise of working near the half-ton mobile devices that direct themselves. According to the workers, these robots produce loud sounds and should only be used for the physical and everyday tasks of the warehouse.
According to Amanda Taillon, a worker at Amazon, these robots are heavy machines, and it becomes hectic to operate these types of equipment. Talking about her job description at Amazon, Taillon said, “I am here responsible for entering a cage and taming Amazon’s wheeled warehouse robots. When I come in, I have to strap on a light-up utility belt, control the closest robots to halt instantly and instruct other robots to slow down or adjust their routes. Talking about her everyday experience, she said, “When you’re out there, and you can hear them moving around, but you can’t see them, it’s like, ‘Where are they going to come from?. It’s a little nerve-racking at first.”
Standing nearby a 6ft-tall fleet and surrounding by roving robot shelves zipped around behind a chain-link fence, Amanda said, “They weigh a lot.” She said so during the pre-Christmas rush at a company warehouse in Connecticut.
With all these comments and reactions, Amazon, along with its rival companies, is demanding its warehouse workers to get used to working with robots. The reason being the pace and productivity provided by these robots. Talking specifically about Amazon, the company owns more than 200,000 drives – the robotic vehicles. Amazon began introducing robotics into its warehouses a few years ago. Shortly before that, Amazon acquired Kiva Systems for $775 million and rebranded it as Amazon Robotics.
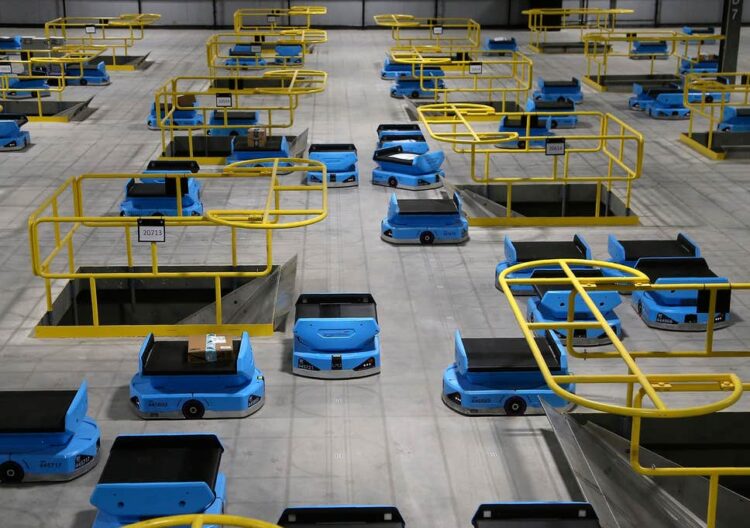
Almost a decade ago, the company had about 100,000 units, and soon in 2014, this number increased to 150,000. These drives are used to move goods through its delivery fulfillment centers around the US.
On the other hand, Shopify – the Canadian e-commerce company bought Massachusetts-based startup 6 River Systems worth $450m (£343m). These systems make an autonomous cart nicknamed Chuck that can follow workers around a warehouse. Not only that, other mobile robot startups are partnering with delivery giants such as FedEx and DHL or retailers such as Walmart.
It is said that without these robotic arms, fast-moving pods, and other forms of warehouse automation, retailers wouldn’t be able to fulfill consumer demand. These robots make the work easier and enable these giant companies to deliver the packages on the doorsteps of the customers in a day or two after the order has been placed.
One thing that should be noted here is that despite this pace of robotization, Amazon continued to recruit new employees. Since the advent of Kiva robots, the company has hired thousands of warehouse employees in the United States alone. Now millions of people are working in warehouses, but soon their number will increase, and work tasks will change.
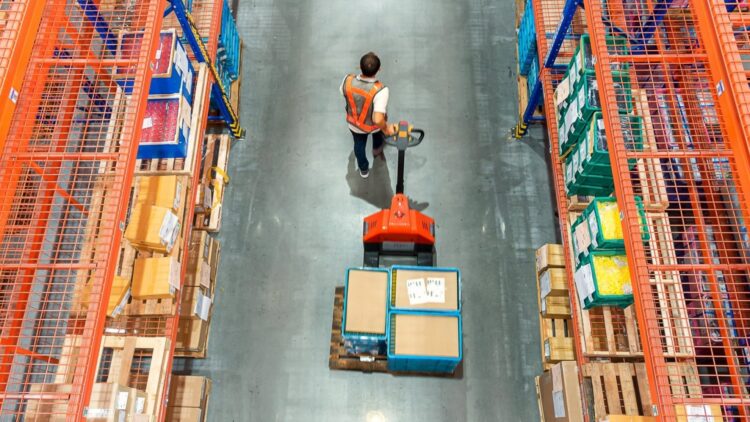
This confirms that the fear of workers about losing jobs has been minimized, yet there are growing concerns about keeping up with the pace of the latest artificial intelligence technology is taking a toll on human workers’ health, safety, and morale.
The addition of robots at the warehouse pressurize workers to speed up their performance as the standards set by robots in term of productivity and efficiency are higher. Hence, this addition of robotics and AI software leads to human burnout at the warehouses.
Amazon Robotics’ chief technologist, Tye Brady threw light on the role of robots and said, “The efficiencies we gain from our associates and robotics working together harmoniously – what I like to call a symphony of humans and machines working together – allows us to pass along a lower cost to our customer.” He added that the engineer ergonomic designs into their system at the initial stage because, for them, the workers’ safety remains their top priority.
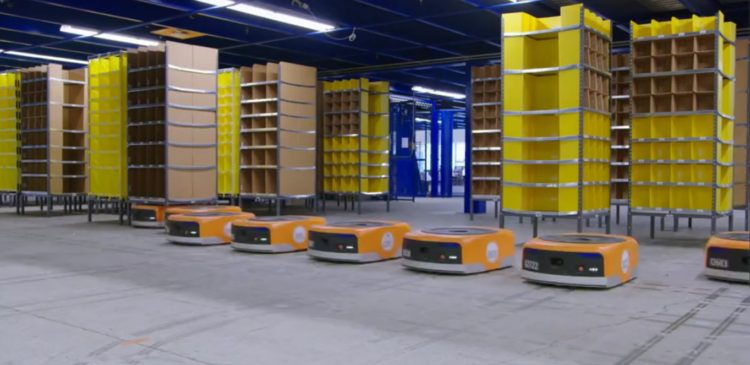
To examine the relationship between robots and workers and the rate of injuries, The Centre for Investigative Reporting published a journalistic investigation report – Reveal. According to this report, the rate of injuries reported at the robot-powered warehouses is higher than those where only humans work. To estimate this fact, Reveal investigated the records of 28 warehouses of Amazon operating in 16 different states. As per the report’s analysis, the rate of serious injuries is more than double the warehousing industry average. The reason behind this is their selection of robots.
If we analyze the overall scenario, the robots being used by rival companies are more human-friendly. This brings down the rate of accidents and makes workers more comfortable. To get more details about these human-friendly robots, visit rozum.com.