Opening Word
In the modern world, business is being done a lot different than it once was. Thanks to the numerous advances in technology, we can now introduce incredible features into a wide variety of business stages and use automation for most of them. This not only makes the job faster and easier but it also greatly reduces the overall costs of manufacturing and operating.
Injection molding is one of the most efficient and effective manufacturing techniques. It allows for fast and affordable production of complex parts, reduces waste, and is generally optimized for sectors that prioritize fast production above all else. Therefore, it is no surprise that most companies in the manufacturing sector are embracing it as the go-to manufacturing technique, welcoming it with open arms into their facilities.
However, since this technique involves using high heat and melted plastic, it carries certain safety risks that can lead to catastrophic workplace injuries no matter how careful everyone is trying to be. These injuries can lead to increased legal costs, heightened levels of workplace compensation claims, low employee morale, a general drop in productivity, and therefore the revenue as well.
All is not grim though as there is some good news too. The above-mentioned risks are quite a problem for human workers, but what about non-human ones? That is right, we mean robots, machines that are specifically developed and programmed to do a certain thing with limited risks or mishaps. By utilizing these amazing creations and simply deploying them to the field, the whole operation of a company or firm will benefit. Make sure to check the solutions made by Universal-Robots, which not only reduce but also eliminate most of the safety risks that are associated with injection molding. In fact, in most of cases, you can even avoid spending money on safety precautions and structures that are typically necessary in order to protect regular human employees. To learn more about this, make sure to read the rest of the article carefully.
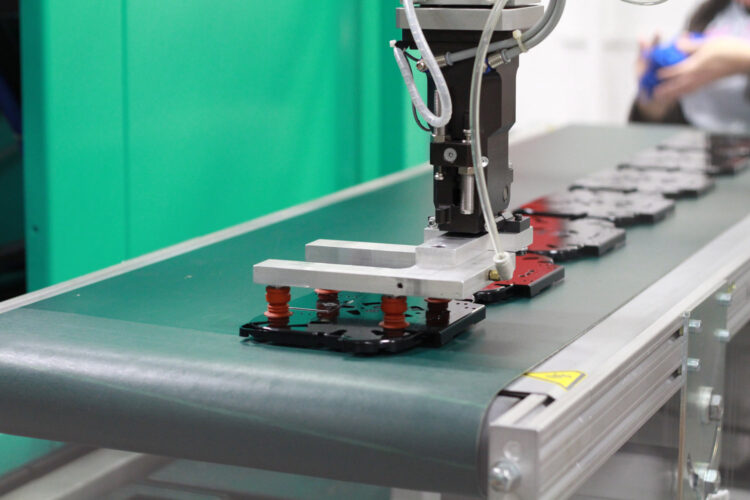
Operator’s gate safety precaution
When an injection molding process is manual or semi-automatic, an operator can easily gain access to the working molding machine or other hazardous areas thanks to the operator’s gate. If this is done while the machine is still running, it creates an immense safety hazard. There is a risk of serious injury, amputation, and / or crushing injuries in case a person gets trapped in between the mold halves or any other of the machine’s larger and dangerous moving parts.
To prevent this from happening, the company has to install hydraulic or electrical interlocks that keep the molds of the machine from closing on someone. Installation of top guards and other safety structures may also be necessary for additional safety. Furthermore, one will have to spend money on training employees with regards to injection molding safety hazards and safety precautions that they should always take.
This is always a smart thing to do no matter how much effort and money you have put into the general safety in the workplace. Your employees should have regular safety training sessions to remind themselves about how best to stay safe in the workplace. Do not try to go around this nor try to save up time and resources by limiting the quality and effect of these presentations.
If you automate most or even all of the main tasks that comprise the injection molding process, increased safety training and an overall mentality of a possible hazard are things that you will not have to worry about every day. Since the robot can execute the tasks nearly flawlessly provided that it is programmed and adapted correctly, it will troubleshoot and even in some cases even fix errors, meaning you will not need employees to operate the machines directly. All they will need to do from time to time is to tend to the robots, clean them and carry out simple checkups. The robots will not need expensive training classes, and you will also not have to worry about installing expensive interlocks or safety platforms. As a result, through automation, you can both minimize exposure to safety hazards, while at the same time avoiding the need to implement costly safety measures for a large number of employees.
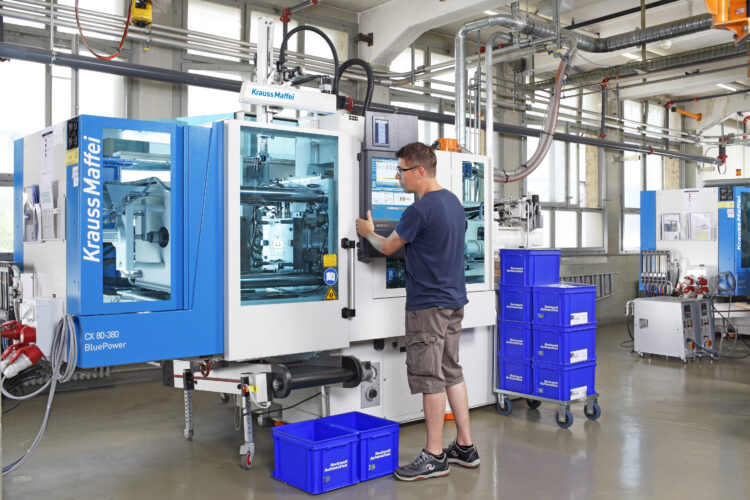
Raw material feeding safety measures
In injection molding processes that are not automated, an employee has to manually feed the plastics into the machine. This presents an array of risk factors that can have catastrophic results. For starters, the employees who are handling this process can easily trip and slip on the raw materials, causing injuries or even death. For the really big machinery, they may have to use tall ladders in order to properly access and feed the machine. This exposes them to the risk of falling in alongside the plastics. These employees run the risk of getting scalded from melted plastic splashes on a daily basis and they can also get burns when they accidentally come in contact with the heated barrel.
To protect against these many risks, you may have to spend extra money insulating the heated surfaces. Guard railing may also have to be installed in order to shield employees from potentially harmful surfaces. Since the use of advanced protective gear like heat resistant work uniforms, PPE, and specialized eye protection is necessary, you will have to allocate money for these expenses and have spare equipment at the ready in case someone damages theirs. You may also have to build rolling stairs, stable ladders, and other safety measures in order to make it safe for employees to access the hopper. All of these things cost money and are sadly overlooked at times in order to cut spending.
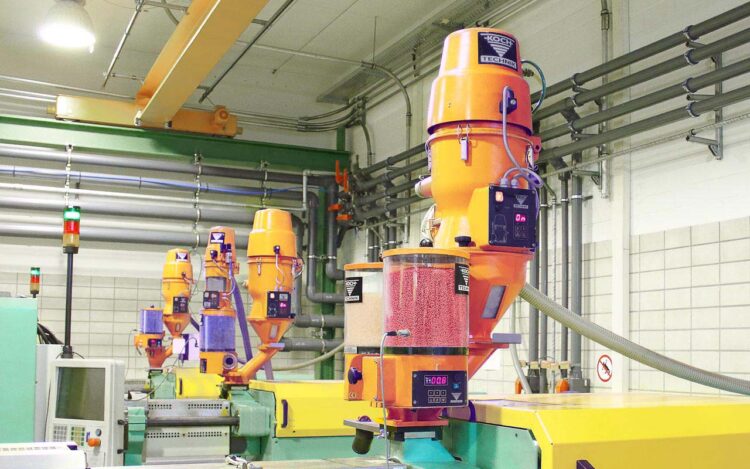
While it is easy to reduce the risks of accidents and injuries by taking these safety precautions, accidents can and will still happen. Even when employees have undergone proper training, they can sometimes forget or even lose concentration and a bad thing can happen in an instant. As a result, taking these costly measures may still not be enough to protect your employees.
Instead of worrying about spending money on making the space safe for human operators, you can simply automate the whole process and limit the number of people you need to run your business. Robots are precise, they never make mistakes, and they can operate in harsh environmental conditions without becoming injured, tired, stressed, or hungry. Using them will, therefore, save you money, both in terms of litigation and also in terms of not having to put in place exhaustive safety measures. It will also make your company much more efficient and give you more revenue at the end of the fiscal year.