The world of manufacturing is undergoing a seismic shift, driven in large part by the rapid advancements in technology. At the heart of this transformation is the IIoT – Industrial Internet of Things. This interconnected web of devices, sensors, and software is revolutionizing how industries operate, paving the way for smarter, more efficient, and highly automated production lines.
According to a McKinsey Global Institute analysis, the adoption of IIoT technologies has the potential to unlock up to $11.1 trillion in economic value globally by 2025. The huge improvements in operational efficiencies, resource utilization, and decision-making processes provided by IIoT contribute to this potential value.
Schneider Electric, a global leader in energy management and automation, is pioneering the use of IIoT. They enable enterprises to monitor real-time data, predict equipment breakdowns, and even automate processes without human interaction by integrating connected devices into their systems. This is about optimizing the entire manufacturing cycle for optimum output with the least amount of waste.
Furthermore, the IIoT is acting as a catalyst for business transformation. Traditional manufacturing models that prioritized walled processes and decisions based on historical data are giving way to models that prioritize real-time insights and cross-functional partnerships. As companies embrace IIoT solutions, we’re seeing a movement away from simply producing items and toward developing integrated services and solutions that provide value across the product lifetime.
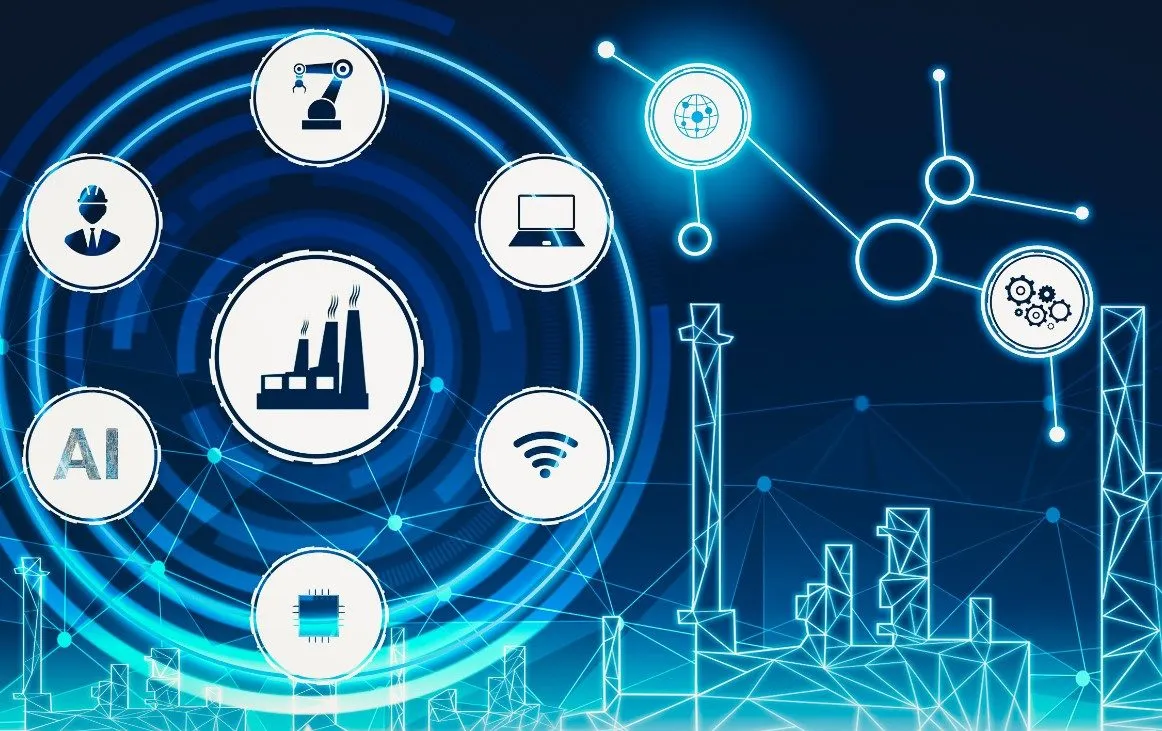
Consider a manufacturing plant that is driven by Schneider Electric’s IIoT solutions. Every machine in this plant is linked and communicates with one another. When one machine identifies a possible problem, it can automatically alter other operations or even order new parts to ensure that production is not interrupted. A decade ago, this level of automation and efficiency would have been inconceivable.
However, it is not all about technology. A culture transformation inside enterprises is also required for successful IIoT integration. Employees must be trained to understand, evaluate, and act on the massive amounts of data produced by IIoT devices. As firms such as Schneider Electric have proved, investing in human capital is just as important as investing in technology in order to fully realize the potential of IIoT.
As industries integrate IIoT solutions further into their systems, cybersecurity becomes more important. According to Cybersecurity Ventures, the annual cost of cybercrime might reach $6 trillion by 2021. The risk of potential breaches becomes a major problem in the area of IIoT, where gadgets are continually interacting. Manufacturers are thus trying not only to optimize but also to secure their operations. Schneider Electric, for example, has built multi-layered security frameworks into their IIoT services to ensure that data integrity and system functionality remain unaffected even in the face of potential cyber threats.
The IIoT’s impact isn’t restricted to a single plant; its implications extend throughout the entire global supply chain. Businesses can monitor items in real-time from the factory floor to the end consumer thanks to advanced sensors and tracking systems. With this level of supervision, inventory management, transportation, and even demand forecasts become more precise. The result is reduced overhead, less waste, and a more efficient supply chain operation. Companies can respond to market shifts faster than ever before, ensuring that supply always meets demand as efficiently as possible.
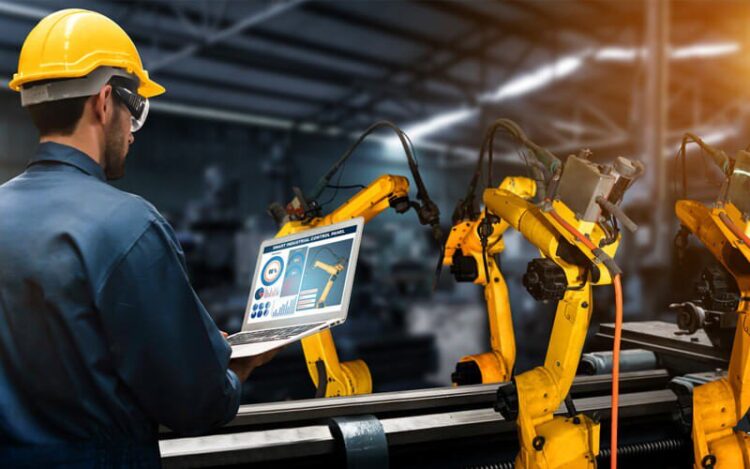
Among the industrial breakthroughs heralded by IIoT is a substantial positive impact on the environment. Industries unintentionally contribute to sustainability by streamlining processes and eliminating waste. Energy consumption, for example, which is a significant financial and environmental concern in manufacturing, can be optimized utilizing IIoT systems. Predictive maintenance, made possible by IIoT, guarantees that machinery operates at optimal efficiency, spending less energy and emitting less pollution.
Furthermore, as resource allocation gets more exact, enterprises will be able to reduce their environmental imprint, resulting in a win not only for businesses but also for the globe.
The Industrial Internet of Things (IIoT) has revolutionized the manufacturing sector, offering unprecedented operational and economic benefits. However, with these advancements come significant ethical considerations, especially concerning data usage.
As IIoT devices continuously gather vast amounts of data, manufacturers must prioritize data privacy and uphold transparency. For instance, a smart factory might collect data on machine performance, employee productivity, and even energy consumption. While this data can optimize operations, it’s crucial to ensure that personal and sensitive information remains protected.
Addressing concerns related to data ownership, obtaining proper consent, and preventing potential misuse is paramount. By doing so, manufacturers can build trust among consumers and stakeholders, ensuring that the benefits of IIoT are not overshadowed by privacy concerns.
The rise of IIoT has ushered in a new era for manufacturing, blending traditional practices with cutting-edge digital technologies. This integration demands a workforce adept in both realms. Manufacturers, therefore, face the challenge of bridging the skills gap. Investing in upskilling and reskilling initiatives is essential. For example, a machine operator might need training in data analytics to interpret insights from IIoT devices effectively.
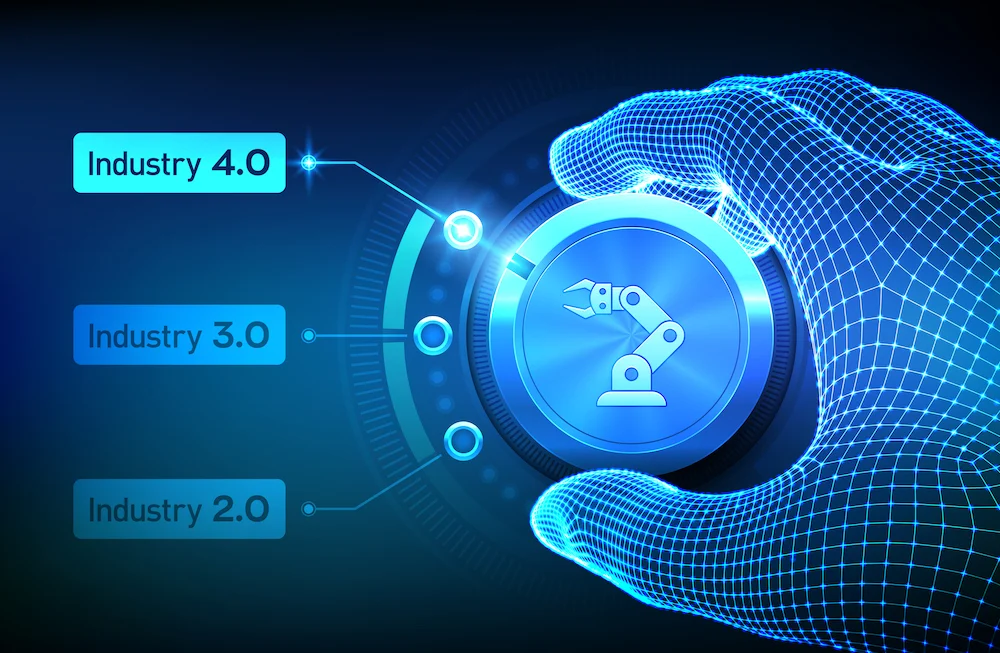
By fostering a culture of continuous learning, manufacturers can ensure that their workforce remains agile, adapting to the evolving demands of IIoT. This not only maximizes the benefits of the technology but also ensures job stability and growth in the industry.
The promise of IIoT is universal, but its implementation can vary based on regional challenges. Industries in developing regions, often grappling with limited infrastructure and resources, might find standard IIoT solutions challenging to adopt.
However, this doesn’t mean they should be left behind in the IIoT revolution. Tailoring localized IIoT solutions that are cost-effective and adaptable to specific regional conditions is the way forward. For instance, a solution designed for a high-tech factory in Silicon Valley might not be suitable for a small-scale manufacturer in a developing country. By understanding and addressing the unique challenges of these regions, we can drive industrial progress at a global scale, ensuring that the benefits of IIoT are accessible to all.
The numerous advantages of IIoT are truly transformational, affecting every aspect of manufacturing, from operational processes and commercial strategies to bigger global supply chains and environmental concerns.
However, as enterprises traverse this new era, a comprehensive approach that includes technological integration, cybersecurity, and environmental stewardship becomes essential. The future of manufacturing promises not only extraordinary efficiency but also a dedication to global well-being and sustainability, with industry leaders like Schneider Electric paving the course.