If you are a process manager or if you work as a business production planner, you are probably aware of how useful and important resource management is. In fact, if you want to be successful in your business, it is a necessary and most important thing to focus on. Although it is critical for operating and functioning properly, a lot of global companies still struggle to manage their resources in order for their production process to meet the demand for their products.
I could state hundreds of examples why not implementing DDMRP is bad for your business, however, we will focus on one particular example. During 2011, Procter and Gamble’s Tide Pods were supposed to be released in America. They set the product launch for late 2011, however, they could not meet that deadline. The product launch was delayed until 2012 due to the company needing more time to boost their production to meet the growing demand for their product. But, the delay only made things worse for them since they dropped significantly on the list of leading companies in the market. And, this is exactly where DDMRP comes in.
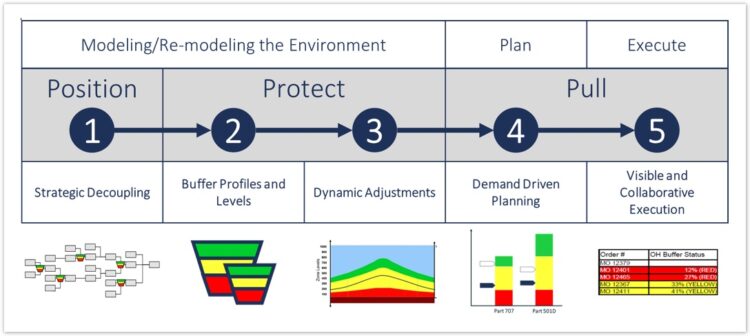
Although you might think that it is simple to execute DDMRP, it does require things like changing the business culture and mentality of the personnel working in the company – especially the managers and planners. There are six categories in DDMRP, however, the sixth one is something that requires both managers and planners to be a bit more open-minded towards implementing a different resource planning strategy. The three stages of DDMRP include: positioning, pulling, and protecting. The parts include setting buffer levels, strategic decoupling, demand-driven planning, dynamically adjusting the buffers, and collaborative execution of orders. Let’s take a look at what this means:
Position
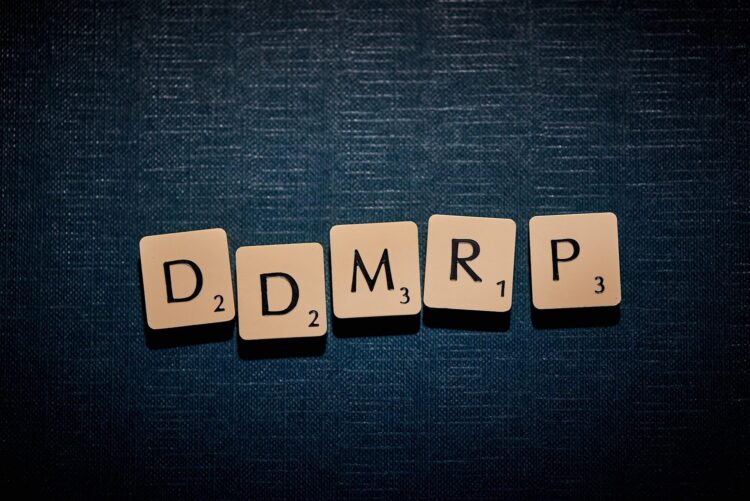
The first thing you will need to do is to strategically create separation points in the supply chain. This should be implemented to lessen the variations in the supply and demand chain and the implementation point will require you to consider several things like process capacity, lead times, and the flexibility of the inventory space. Production supervisors and planners need to set these points where they can boost the adaptability and compression of lead times. Then they can use DDMRP programs that will manage the chain by segments instead of looking at the entire lead time.
Protect
According to the experts from Demand Driven Technologies, in order to protect the supply chain, a buffer needs to be incorporated into every separation point. They will hold the inventory when preparing for the next stage of the supply chain. To determine the inventory amount that is permitted in one buffer, you will need to calculate it with a formula that looks at lead times, as well as the average daily use of materials. This system will allow planners to know when the inventory needs to be filled again.
Pull
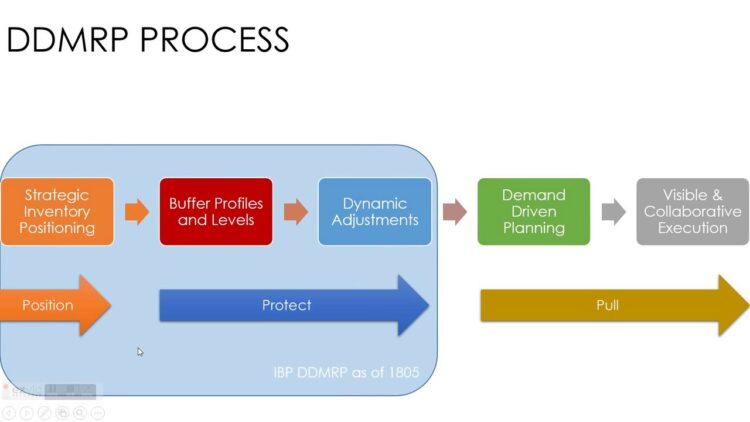
One of the things that make DDMRP different than MRP is that there is a focus on customer demand. What this means is that the orders are generated if there is a demand, instead of predicting leads and orders. The demand is only visible when the order is made, hence, you will be able to prevent understocking or overstocking which will keep the production process in optimal condition.
Conclusion
While DDMRP is not used by all companies, it does prove effective methods of allowing businesses to adjust to the ever-changing markets. There are brands that benefited quite a lot from this – including Coca Cola and British Telecom – hence, it is not just a buzzword, it actually works.